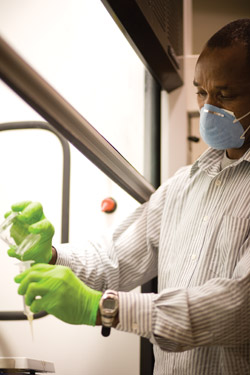
opens. At Wichita State, a grand expansion is under way.
The process of electrospinning, shown here by doctoral
student Adanij Adebayo, creates micro and nano fibers:
strands similar to a spider web but 10 times smaller.
For the WSU College of Engineering and the National Institute for Aviation Research, new space equals profit — not just monetary profit, but the profit in knowledge that comes from broadening research and educational opportunities.
There will always be uncharted territory in the world of engineering, and that’s why the two new research buildings on campus are so important to Wichita State’s growth.
In the past few months WSU has added 13 labs, 10 at the College of Engineering, three at NIAR. These additions have added nanotechnology and indirect lightning effects to WSU’s areas of expertise. Both subjects are new to the university and are quickly making their way into the classroom and out into the industry.
“We are exposing students to the technology of the next two decades,” says Zulma Toro-Ramos, dean of the College of Engineering. “In terms of business, these are unique labs for most companies. By using our lab first they don’t have to invest in the equipment until they are sure they’ll need it.”
Providing services to industry and education to students isn’t new to WSU, of course. NIAR was founded with the idea of strengthening the research services offered to the aviation industry.
Today, it is ranked fourth in aeronautical research and development expenditures by the National Science Foundation. That’s why John Tomblin, executive director of NIAR, constantly strives to bring innovative research to WSU.
“Every time we add a new field of expertise, we increase our ability to provide the aviation industry with cutting-edge research,” he says. “With the addition of the environmental laboratories, and the new research building, the potential for growth is substantial.”
A Knack for Nano
Nanotechnology is a field of study best suited for individuals who know a little bit of everything. If you take a little chemistry, a bit of physics, some materials sciences and even some mechanical and electrical engineering you’ll find yourself immersed in a science all its own. What that means in terms of research is a field of study that will find solutions to some of the world’s biggest challenges. From fighting deadly diseases, to building stronger and lighter aircraft, nanotechnology is changing the face of the earth one atom at a time.
At WSU, assistant professor Ramazan Asmatulu, two doctoral students — Adanij Adebayo and Waseem Kahn — and 25 members of the university’s Introduction to Nanotechnology class are exploring the possibilities this field of study has to offer.
Nanotechnology effects things on a scale between one and 100 nanometers, which is from the size of a water molecule to a tenth the size of a typical bacteria. It is very, very small scale. But with very, very big potential. So much potential that WSU has created a nanotechnology lab in the university’s new Engineering Research Laboratory Building. Nanotechnology will, Asmatulu says, have strong implications for industries already in the Wichita area, such as aircraft manufacturing, corn based bio-fuel production (ethanol), agriculture and wind power.
Asmatulu, who teaches in the mechanical engineering department, and his students are exploring the process of electrospinning. This process creates micro and nano fibers: strands similar to a spider web but 10 times smaller.
To create these micro fibers, two solutions are dissolved and put into a syringe. The syringe is then pumped with a constant pressure that pushes the fluid evenly to the tip where the fibers form.
As the fibers form at the tip of syringe, an electric charge is applied. This charge creates an electric field, which allows the strands to “spin” toward a collector target, such as a mesh wire. As they travel to the mesh wire, the strands stretch to an extremely small size. After the spinning process, the solvent evaporates and the polymer solidifies, leaving behind nano scale polymeric fibers.
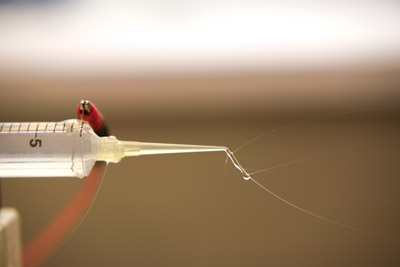
fibers. A syringe filled with two solutions is pumped with
a constant pressure that pushes the fluid evenly to the
top where the fibers form. The attached wire creates an
electric field, which allows the strands to “spin” toward
a collector target.
This is just one of the many areas of testing and research being performed at the lab. Students are also conducting tests in areas such as nanoparticle, nanowire, nanofilm, nanocomposite, nanotube as well as nanotechnology application on solar cell fabrication.
“In this lab, our undergraduate and graduate students will learn nanotechnology to improve their skills, which will also improve their job-finding opportunities and leadership in the near future,” Asmatulu says. “We strongly believe that lab experiments on nanoscale research and development are essential for engineering students to enhance their practical knowledge after fundamental concepts.”
All of this advanced testing requires the latest equipment. There are two pieces of equipment important to nanotechnology research. This includes an atomic force microscope, a high resolution scanning probe microscope that can literally move atoms on a variety of surfaces. The lab is also equipped with a transmission electron microscopy, a light microscope that beams electrons through a specimen to display a magnified image. Asmatulu estimates the nanotechnology laboratory will be completely functional by January 2008.
Utilizing this equipment enables the university to take a step into future nanotechnology research. “WSU is located in a metropolitan city and has strong industrial activities,” Asmatulu says. “Both the university and the city will have great benefits from the nanotechnology laboratory."
Environmental Effects
NIAR offers the capability to conduct lots of testing under one roof. For many companies, the cost of buying test equipment is enough to put them out of business. By not only making testing affordable but by having qualified staff and equipment in one place is what makes NIAR successful. The new environmental laboratories are no exception. In May, the Susceptibility Test Lab opened its doors, in June the Indirect Lightning Test Lab hosted its first client and in August the Environmental Test Laboratory began equipping itself for clients.
These are the first NIAR labs to focus solely on DO-160 certification, guidelines developed by the Radio Technical Commission on Aeronautics. DO-160 certification is not required, but is recommended. Each lab focuses on specific sections of the DO-160 guidelines.
The Indirect Lightning Test Lab saw its first real action in June — literally. Electromech, a Wichita-based custom design and manufacturing facility, was the lab’s first client. Over the course of a week, the company performed lighting induced transient susceptibility certification tests on a flap system for the Quest Kodiak, a turboprop airplane manufactured by Quest Aircraft Co. In this particular test, they are trying to simulate the internal effects of a lightning strike during an aircraft flight. This is just one of the methods used to determine if the equipment installed in the aircraft will be able to withstand a lightning strike and still meet flight safety standards.
Because of the voltage required to run lightning strike tests, the lab is equipped with an observation room. When a test begins, the doors are locked automatically, prohibiting anyone from entering. “When you induce lightning, you have voltage of around 4,000 amps,” says Wade Davis, manager for all of the environmental test laboratories. “We could actually kill people in this lab.”
The Susceptibility Test Lab performs testing related to the capability of aircraft systems, such as a piece of equipment’s ability to operate properly with the magnetic field of another aircraft system or to withstand a voltage spike. This lab hosted its first customer, ICE Corp. of Manhattan, Kan., in April.
Other areas the environmental labs will test include the effects of temperature, humidity, altitude, water, fungus, vibration, explosion, sand, dust, salt spray, shock and crash on aircraft equipment. While some of these areas are currently covered, others won’t be available until after Nov. 6, when NIAR’s Laboratory Engineering Test Facility is scheduled for completion.
Out with the Old
Discovering new ways of looking at old techniques is often rewarding, whether it’s changing how to build airplanes or helping save the environment. Even though Friction Stir Welding was patented by the Welding Institute in England in 1991, its impact on the U.S. aviation industry over the past few years prompted NIAR to create the Advanced Joining and Processing Lab, which opened in 2004 and to install a Friction Stir Welding machine in 2005.
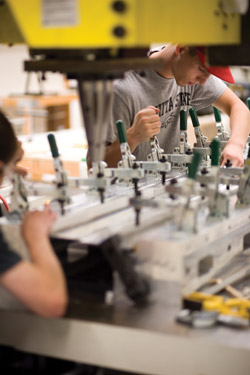
together two pieces of aluminum in preparation
for friction stir welding at WSU’s Advanced
Joining and Processing Lab.
A monstrous piece of equipment, the FSW machine performs the most delicate of tasks — it uses a probe to “stir” two materials together. The thermo-mechanical process uses heat generated from friction and mechanical stirring to soften the material, rather than melting the materials together, as is done in conventional fusion welding processes.
This joining process is well suited for both long continuous welds and spot welds in aluminum and is being developed to replace rivets on aircraft. Friction stir welding has a number of advantages over current fastened and welded joints, including increased strength and reliability, reduced manufacturing time, and lower costs.
“Friction stir welding is posed to create a paradigm shift in manufacturing technology,” says Christian Widener, a research scientist in the Advanced Joining Lab. “U.S. manufacturers are going to be forced to adopt this technology in order to remain competitive.” WSU’s lab has three full-time employees and 14 graduate and undergraduate students.
While one lab explores how to change the technology that builds our transportation systems, another — the Sustainable Engineering Systems Laboratory at the College of Engineering — looks at how we can sustain our environment through technology.
“We are trying to find a way to minimize the impact that other technologies might have on the earth,” says Jan Twomey, assistant professor in industrial and manufacturing engineering. “Everything has an input on the earth: energy, water; and an output: pollution, emissions, waste.”
The other eight labs established at the Engineering Research Laboratory Building provide students and faculty members with the opportunity to study everything from robotic aircraft assemblies being manufactured for the next generation of aircraft (in the new robotics lab), to determining the flammability of the material in an airplane (in the fuel and fire safety lab).
For WSU engineering students, the possibility of obtaining hands-on experience is unlimited. For aviation and other industries, the world’s most cutting-edge research can be found just inside the doors of NIAR and the College of Engineering.